Engineering Chains in Automated Car Wash Systems
In today's automated car wash systems, performance, durability, and corrosion resistance are essential. While standard roller chains are used in some setups, most modern, high-throughput, or heavy-duty wash tunnels rely on specialized engineering chains. These chains are designed to handle extreme conditions—frequent water exposure, chemical sprays, abrasive debris, and constant motion.
Below are the most common types of conveyor chains for car wash applications, engineered for strength, longevity, and smooth integration with conveyor components.
1. Welded Steel Chains
Welded steel chains are a go-to solution for high-capacity wash systems. Built with welded links, they offer superior tensile strength and durability in environments where sand, gravel, and vehicle residue are common.
● Advantages: High strength, excellent shock resistance, durable in dirty or abrasive settings.
● Best for: Tunnel-style automated car wash systems that service large vehicles like trucks and SUVs.
● Typical Use: Driving the main chains for car wash in commercial operations with heavy vehicle traffic and debris.
2. Drop-Forged Rivetless Chains – Featuring the X458 Chain
For more advanced or complex conveyor layouts, drop-forged rivetless chains are the preferred choice. These engineering chains are known for their flexibility, ease of maintenance, and high load capacity. Among them, the X458 drop forged rivetless chain stands out as the industry standard.
Why CamelConvey X458?
The X458 drop forged rivetless chain is engineered to deliver long-lasting performance in even the most demanding automated car wash systems. Its robust forged steel design allows for reliable movement across curved or multi-stage conveyors, while its rivetless construction enables quick link replacement with minimal downtime.
● Advantages: Exceptional durability, easy to install and repair, compatible with a wide range of conveyor components.CamelConvey offers specially designed X458 attachment link to assist the use of X458 chains in car wash systems and improve stability.
● Best for: Multi-directional wash tunnels, curved conveyor layouts, and high-frequency operations.
● Example Application: Powering the full conveyor path in a tunnel wash system that requires smooth transitions between pre-soak, wash, wax, and drying zones.
3. Combination Chains
Combination chains are a hybrid solution that integrates cast or forged elements with steel sidebars for enhanced strength and versatility. These engineering chains are often customized with attachments to serve specific functions within a car wash conveyor.
● Advantages: Highly customizable, rugged, and built for repetitive exposure to harsh chemicals and moisture.
● Best for: Express or custom wash systems needing add-ons like pushers, rollers, or vehicle alignment guides.
● Typical Use: Operating conveyor chains for car wash systems with specialized requirements, such as guiding wheels or engaging pusher dogs.
How Engineering Chains Overcome Challenges in Car Wash Environments
Automated car wash systems present a uniquely harsh operational environment. Thanks to their robust materials and precision engineering, engineering chains are well-equipped to handle the following challenges:
1. Constant Moisture
Regular chains tend to rust when exposed to water. However, stainless steel or corrosion-resistant coated chains are specifically designed to prevent oxidation and maintain functionality over time.
2. Chemical Corrosion
Detergents, foaming agents, and waxes can degrade typical metal chains. High-quality conveyor chains for car wash use specially formulated materials to maintain structural integrity despite continuous chemical exposure.
3. Abrasive Debris and Contamination
Vehicles often carry dirt, sand, and gravel into the system, which can increase wear on the chain. Heavy-duty options like combination chains and drop-forged chains offer enhanced resistance to abrasive damage.
4. High Throughput Demands
Commercial car wash systems frequently process thousands of vehicles per day. Chains must support long-term, high-cycle operation while minimizing downtime and maintenance needs. For example:
● In high-traffic tunnel washes processing up to 100 vehicles per hour, stainless steel roller chains or welded steel chains are ideal for withstanding continuous water jets and chemical sprays while maintaining smooth conveyor function.
● In multi-stage, complex conveyor layouts, drop-forged rivetless chains, when used with adaptable conveyor components, provide the flexibility and strength needed to handle sharp turns and directional transitions without sacrificing durability.
Maintenance Tips for Engineering Chains in Automated Car Wash Systems
To ensure optimal performance and long-term durability of engineering chains, sprockets, and conveyor chains for car wash systems, consistent maintenance is essential—especially in the demanding environment of modern automated car wash systems. Neglecting basic upkeep can lead to system failures, costly downtime, and safety hazards. Below are expert maintenance tips to keep your chain-driven wash system running smoothly:
1. Perform Routine Inspections
Inspect your chains at least once a week. Look for signs of wear such as elongation, rust, misalignment, or worn sprocket teeth. Pay particular attention to attachments and link integrity—especially when using high-performance chains like the X458 drop forged rivetless chain, which must remain in top condition for optimal performance.
2. Clean After Each Cycle
After every wash cycle, remove soap residue, wax, sand, and debris from chains and sprockets. Accumulated chemicals and contaminants can accelerate corrosion, particularly in steel components. Proper cleaning extends the life of both engineering chains and mating components.
3. Use the Right Lubrication
For non-self-lubricating chains, apply water-resistant lubricants designed specifically for wet, high-humidity environments. This is especially important in tunnel-style automated car wash systems, where chains are continuously exposed to moisture.
4. Maintain Correct Chain Tension
Check chain tension regularly. Over-tightening can lead to premature wear on sprockets and chain links, while slack chains risk derailment or uneven loading. Whether you're using standard roller chains or heavy-duty solutions like the X458 drop forged rivetless chain, proper tension is critical to safe and efficient operation.
5. Replace Worn Parts Immediately
Don't wait for a breakdown. Replace damaged chains, sprockets, or worn conveyor components as soon as wear is detected. For systems using rivetless designs like X458, keep spare links on hand for quick repairs and minimal downtime.
6. Account for Environmental Conditions
In coastal regions or areas where road salt is prevalent, corrosion risk is significantly higher. In these conditions, choose stainless steel or specially coated engineering chains to ensure system reliability. Chains like the X458 drop forged rivetless chain are available in corrosion-resistant variants to meet these challenges head-on.
Built to Perform in the Toughest Car Wash Conditions
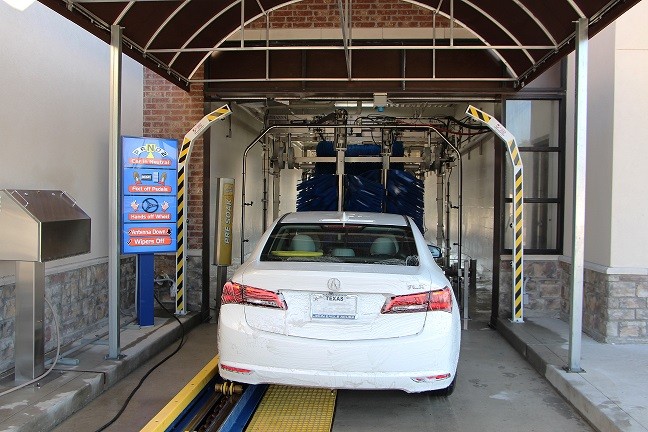
Whether dealing with constant water exposure, corrosive detergents, or vehicle-borne debris, engineering chains must be equipped to handle the full spectrum of challenges found in automated car wash systems. From welded steel chains to combination chains, each type can be further enhanced with corrosion-resistant coatings to maximize service life.
However, when it comes to all-around performance, reliability, and ease of integration with modern conveyor components, the X458 drop forged rivetless chain is the top-tier solution. Its strength, flexibility, and field-proven design make it the ideal choice for operators looking to reduce maintenance and keep their wash lines running efficiently.